Can You Add Acetone to Polyurea Basecoat? Risks and Safer Alternatives
Adding acetone to the polyurea basecoat is not a good idea. While this might seem like a quick and easy solution, it can actually do more harm than good.
Some installers attempt to use acetone to thin polyurea or extend working time, this shortcut can weaken the coating, cause surface defects, void warranties, and lead to inconsistent results.
Instead, industry professionals recommend safer alternatives like manufacturer-approved reducers and environmental adjustments to ensure a durable, high-performance flooring system.
In this guide, I’ll break down why acetone is a risky choice, explore its negative effects on polyurea, and highlight the best alternatives for a professional-grade installation.
Understanding Polyurea Basecoats
Polyurea floor coatings are widely used in commercial, industrial, and residential flooring systems due to their fast curing times, high durability, and resistance to chemicals and abrasions.
These concrete floor coatings provide a long-lasting, high-performance surface ideal for spaces with heavy foot traffic or machinery.
Polyurea Basecoat
One of polyurea’s key advantages is its rapid curing properties. However, this speed can also be a challenge for installers who need more time to evenly apply the basecoat before broadcasting high-quality vinyl flakes.
To slow down curing, some professionals attempt to thin polyurea with acetone—but this approach can lead to significant problems.
The Hidden Dangers of Adding Acetone to Polyurea Coatings
1. Weakened Coating Strength
Adding acetone to polyurea disrupts the chemical composition of the material, weakening the polymer structure that provides strength and durability.
Flooring specialists warn that even small amounts of acetone can lead to reduced impact resistance and premature wear, especially in high-traffic areas where durability is critical.
2. Solvent Popping and Surface Imperfections
Acetone evaporates at a much faster rate than polyurea is designed to handle.
This rapid evaporation can cause solvent popping, a phenomenon where tiny air bubbles become trapped within the concrete floor coatings.
As the acetone escapes too quickly, these bubbles turn into blisters, pinholes, or an uneven surface texture.
Experts in industrial flooring note that solvent popping not only affects appearance but also creates vulnerabilities that allow moisture and contaminants to penetrate, leading to long-term structural damage. These imperfections significantly reduce the protective qualities of the flooring system, increasing maintenance costs over time.
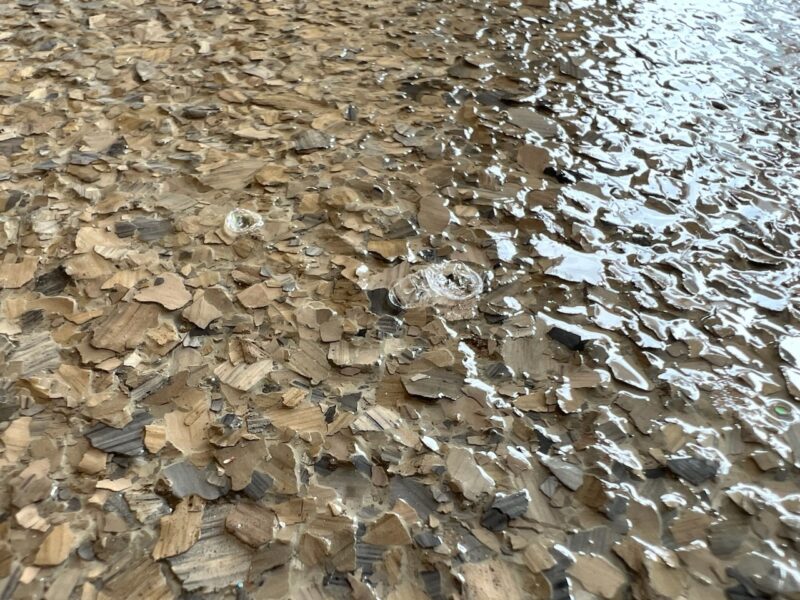
Concrete surface imperfections
3. Warranty Voids & Compliance Issues
Most polyurea manufacturers explicitly state in their Technical Data Sheets (TDS) that their formulas do not require external additives. Adding acetone:
- Alters the product’s chemical balance
- Can void manufacturer warranties
- Risks compliance issues for professional installers
This means if something goes wrong—peeling, bubbling, or premature wear—you may not be covered for repairs or replacement.
4. Inconsistent Performance
Unlike manufacturer-approved reducers, acetone use introduces variables that can result in unpredictable curing behavior.
The amount of added inconsistencies in the application, and weather conditions can affect concrete floor coatings. These can all lead to problems such as uneven curing, discoloration, and poor adhesion of vinyl chips.
Concrete coating specialists advise that professional installers should follow data sheet recommendations to ensure a uniform finish. Acetone-thinned polyurea is more likely to cure unevenly, leading to color variations and weak adhesion that shorten the lifespan of the flooring system.
Safe and Effective Alternatives to Acetone
If you need to extend the working time or adjust viscosity, here are better solutions that maintain the integrity of your flooring system:
1. Use a Manufacturer-Approved Reducer
Many polyurea manufacturers offer their own reducers or solvents specifically designed to modify the working time of their concrete floor coatings without compromising integrity. These products are formulated to maintain proper adhesion, curing properties, and durability while giving you additional time for application.
2. Work in Smaller Sections
Rather than trying to extend the working time of the entire batch, consider working in smaller sections. This allows you to maintain better control over the application and ensures a smoother, more even surface.
Contractors recommend this approach, particularly for large flooring projects, as it minimizes waste and ensures a more precise application of the basecoat.
3. Adjust Temperature and Humidity
Since environmental factors impact curing times, flooring experts recommend installing coatings in cooler temperatures and controlling humidity levels in the workspace to naturally slow the curing process.
4. Use a Slower Curing Polyurea Formula
Some polyurea formulations are designed with slower curing times. These are ideal for situations where extended workability is needed. Check with your supplier to see if a slower curing version is available.
Best Practices for Installing Polyurea Basecoats
To ensure a successful flooring installation, follow these best practices:
- Surface Preparation: Properly clean and enhance the floor surface with concrete grinding equipment before applying the basecoat. Any dust, grease, or moisture can affect adhesion.
- Proper Mixing: Follow the manufacturer’s instructions precisely—do not add unauthorized solvents or chemicals.
- Application Techniques: Use the recommended tools, such as rollers or sprayers, to achieve an even coat without overworking the material.
- Timing Matters: Broadcast vinyl flakes immediately after applying the basecoat for seamless integration.
- Curing Compliance: Allow the basecoat to cure according to manufacturer’s guidelines before applying a topcoat or sealant.
Invest in the Right Training & Products
For contractors looking to improve their skills and avoid costly mistakes, vinyl chip training for flooring installation is essential. Learning about proper techniques, tools, and materials ensures:
- Professional-quality installations
- Compliance with manufacturer guidelines
- Fewer call-backs or costly rework
By investing in training and using a manufacturer-approved concrete coatings supply, you can achieve durable, high-performance floors without taking shortcuts that compromise quality.
Allsource Supply Inc. Vinyl Chip Training
Conclusion: Prioritize Quality Over Shortcuts
While adding acetone to a polyurea basecoat might seem like a convenient way to slow curing, it introduces significant risks, weakening durability, causing surface defects, voiding warranties, and leading to inconsistent results.
Instead, choose safer, manufacturer-approved solutions like reducers, controlled working conditions, and slow-curing formulations.
If you’re unsure about modifying your products, always refer to the Technical Data Sheet (TDS) or consult with your supplier.
By following industry best practices, you can ensure long-lasting, high-performance flooring installations without unnecessary risks.
Need expert guidance or high-quality concrete floor supplies? Contact our team at Allsource Supply Inc. at 833-663-4255 today!