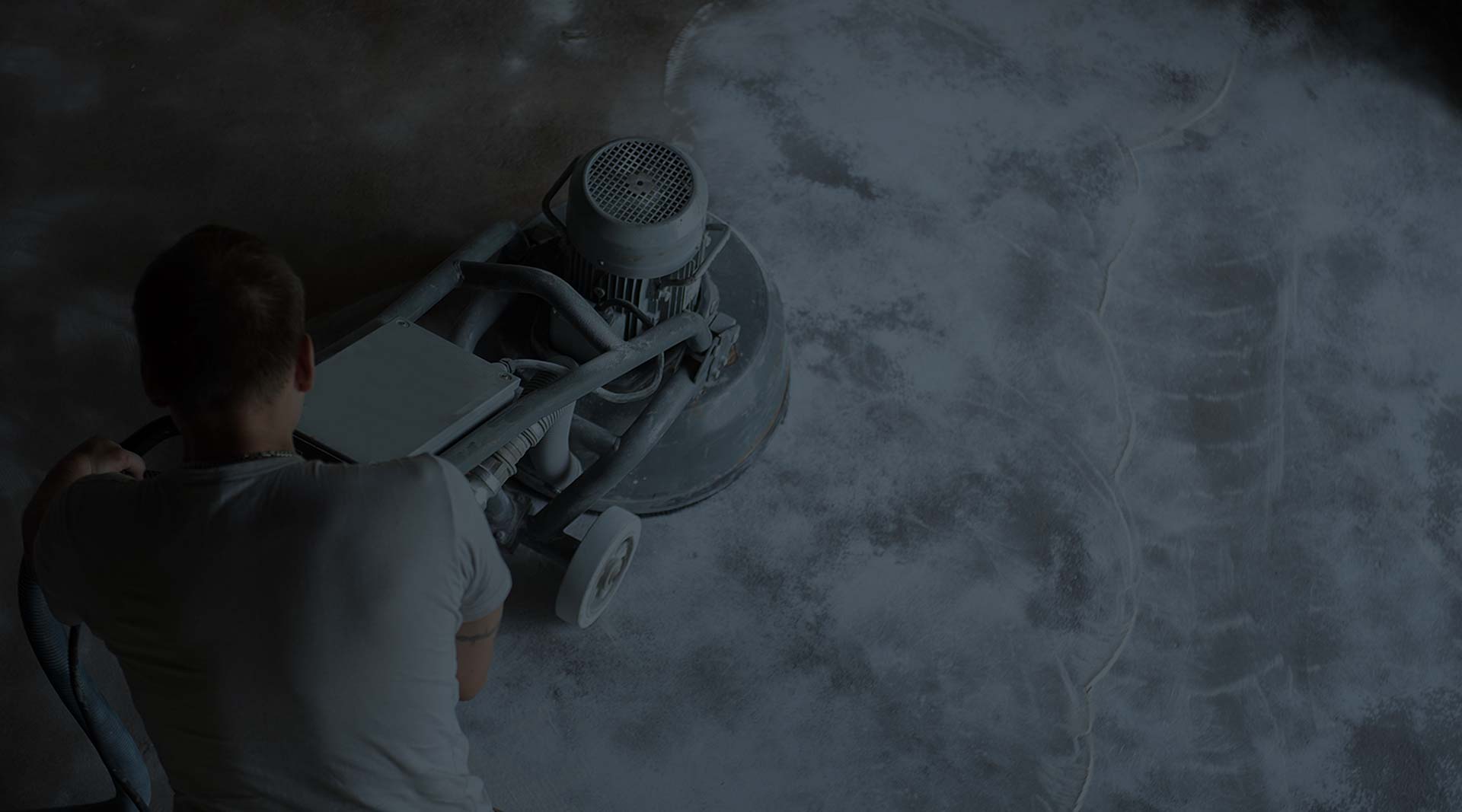
Concrete Moisture Control: Preventing Damage and Ensuring Concrete Durability
In the realm of construction and maintenance, mastering the art of concrete moisture control is paramount. As we delve into the intricacies of this crucial practice, we uncover the key strategies to avert damage and guarantee the lasting durability of your concrete structures. Whether you're a seasoned contractor or a DIY enthusiast, understanding how to effectively manage moisture within concrete is a skill that can save you time, resources, and headaches.
In this article, we'll explore the essential techniques and insights that contribute to the long-term success of your concrete projects. Read on at allsourcesupplyinc.com to fortify your knowledge and ensure the resilience of your construction.
Understanding Concrete Moisture Control
Concrete is a porous material and can absorb moisture from various sources like rainwater, groundwater, and even humidity in the air. This moisture present in concrete acts as a breeding ground for mold and bacteria, which can degrade the integrity of the structure and weaken its durability. Therefore, it's important to understand and implement proper concrete moisture control measures to prevent any long-term damage.
Concrete moisture control refers to the process of managing moisture within concrete structures to ensure their longevity and durability. It involves using various products and techniques that are designed to prevent high levels of moisture from affecting the quality of concrete structures. Effective moisture management not only keeps buildings safe but also ensures cost efficiency by avoiding costly repairs or future material replacements.
Imagine constructing a single-story retail building that incorporates new flooring systems over slabs on grade. Due to a lack of adequate evaluation for moisture-related performance, after installation, the flooring materials begin failing in several locations with coatings de-bonding or peeling off. In this scenario, effective and proper concrete moisture control could have prevented such an incident from happening.
Now that we understand the importance of concrete moisture control, let's take a look at some of the key reasons why moisture seeps into concrete in the first place.
- According to the US Department of Energy, a properly installed vapor barrier can reduce the amount of water that passes through a concrete slab by as much as 99.9%.
- Data from the American Concrete Institute stipulates that an appropriately installed drainage system can lower the risk of moisture-induced damage in concrete structures by up to 85%.
- A report by the National Ready-Mixed Concrete Association revealed that the use of admixtures and sealers can increase the lifespan of concrete structures by implicitly reducing moisture permeation, contributing to an overall increase in durability of 40–60%.
Key Reasons for Moisture in Concrete
Moisture intrusion into concrete structures can occur due to numerous factors, including:
One of the most notable reasons why moisture problems occur in industrial and commercial concrete structures is that they are built under tight deadlines on rushed projects. This means workers tend to skip or overlook crucial steps or vital processes, leading to inadequate curing conditions that leave concrete further exposed to environmental elements.
Hydrostatic pressure—water infiltration through structural walls—is another cause for concern since it increases capillary absorption within porous concrete surfaces.
Pouring concrete during cold weather affects the rate of curing, potentially leading to moisture retention within the material. The result is increased shrinkage after it has cured, allowing for water penetration.
After heavy rainfall or snow thaw periods, ground swells cause an upward movement in pourous slabs on grade, impacting their structural integrity and durability due to excess moisture. This is reason enough to ensure concrete moisture control measures are in place to prevent such incidents.
Proper concrete moisture control takes a methodical approach, implementing practices for keeping structures safe from the harmful impact of excess moisture by preventing any fungal or bacterial growth within porous materials.
Now that we have examined some reasons why moisture seeps into the concrete, let's explore how excess moisture can impact the durability of concrete structures.
The Impact of Moisture on Concrete Durability
Moisture is one of the biggest enemies of concrete, as it can cause significant damage, reducing the lifespan and durability of structures. When moisture penetrates the porous surface of concrete, it reacts with the minerals in the cement, causing them to expand and deteriorate over time. This can result in several problems, including cracking, spalling, and delamination, ultimately leading to costly repairs or even replacement.
For instance, consider a bridge that was constructed in a region with high humidity levels. Over time, moisture seeped into the concrete surface, causing it to crack and weaken. Eventually, the bridge had to be closed down for repairs, costing millions of dollars and causing major disruption to traffic flow. This is just one example of how important it is to control moisture levels in concrete structures.
Moreover, excessive moisture in concrete can also accelerate the growth of mold, mildew, and other fungi, which not only compromise structural integrity but also pose health hazards to those exposed to them.
However, there are arguments by some that a little bit of moisture should be allowed in concrete structures, as it helps maintain their strength and protects them from drying out too quickly. This counterargument undervalues the damaging effects of moisture on concrete, as studies show that even small amounts can adversely affect the quality and lifespan of concrete structures.
In light of this development, it's crucial to implement effective measures for moisture control within concrete structures. Therefore, let's move forward to discussing different strategies for effective moisture mitigation.
Importance of Testing Moisture Levels
When installing new flooring, one error that most contractors make is failing to conduct adequate moisture testing thoroughly. As simple as it may seem, moisture testing is a crucial aspect of any project, as the presence of excessive moisture can lead to severe damage to your structure.
Concrete slabs often have an inherent tendency to hold and develop excess moisture, which could eventually lead to mold growth or even compromise the structural integrity of the building. Mold accumulation may, in turn, cause health concerns for the occupants of that area. Such problems make it necessary to conduct thorough assessments concerning moisture, especially if you are considering installing a floor coating or a new layer of flooring.
One of the commonly used methods of measuring the level of moisture in concrete structures is through moisture vapor emission testing. This method measures the rate at which water vapor passes through the concrete slab and indicates whether additional moisture mitigation is required.
In most cases, the common question asked by contractors is, “When should I test for moisture”? The right answer depends on several factors, such as construction history, location, and environmental conditions.
Some experts suggest that ideally test for moisture after seven days, while others advise waiting 28 days after completion. Though there's no definitive answer to this question, it’s best to base your decision on specific industry standards and guidelines. For example, ASTM International has issued regulations requiring concrete professionals to always perform moisture tests before installation commences.
Moisture testing helps determine existing issues with your new construction project; it's akin to visiting a doctor for regular check-ups. It's easier and cheaper to fix small issues early on that could potentially turn into bigger, more costly issues down the line.
Effective prevention strategies backed up with accurate measurements will go a long way in mitigating any future damage associated with excess moisture buildup on your concrete surfaces. Next up, we discuss some case studies showcasing how proper moisture control ensures longevity for your concrete structures.
Effective Moisture Mitigation Systems
As previously mentioned, moisture control is imperative for maintaining optimal longevity and reducing maintenance costs associated with damaged concrete structures. There are various ways one could mitigate moisture penetration in (and onto) a freshly poured slab or an already existing structure.
An effective moisture mitigation system can prevent moisture from penetrating concrete structures.
One way to control moisture penetration in concrete is to install drainage systems that effectively divert water away from the structure. This includes installing gutters, surface drains, and underground pipes, or adding slopes away from the site.
Another strategy involves using weatherproof materials for construction, such as water-repellent admixtures, sealants, or coatings. These materials actively prevent moisture from infiltrating concrete structures and are especially crucial during rainy seasons when moisture levels are at their peak.
However, the use of protective coatings alone may not suffice in certain situations, such as high groundwater conditions. In such cases, a vapor barrier is placed under the slab to provide additional protection against rapidly concentrated amounts of water. While this method may increase costs in the short term, it's undeniably cheaper than having to replace an entire structure due to moisture damage.
It is, however, important to note that one should not just stop applying any method of controlling moisture but ensure that they implement only approved measures guaranteed by experts in the field.
Drainage, Weatherproofing, and Protective Coatings
One of the most effective ways to prevent moisture damage to concrete is through proper drainage. Proper drainage systems can direct water away from concrete slabs and structures, reducing the amount of moisture that comes into contact with the concrete over time. Poor drainage, on the other hand, can lead to standing water that weakens concrete and causes it to deteriorate faster.
Weatherproofing and protective coatings can also help mitigate moisture damage to concrete. These coatings act as a barrier between the concrete and any external sources of moisture, preventing water from penetrating the surface. Protective coatings are especially important for outdoor structures such as parking garages or bridges that are exposed to harsh weather conditions.
For instance, W.R. Meadows’ PC2R Protection Course is an innovative product designed to provide durable protection for plaza decks, parking garage decks, and roof terraces. This easy-to-install product acts as an underlayment for waterproofing membranes or as a temporary support system during construction. It contributes to extending the lifespan of finished surfaces by reducing freeze-thaw cycling damage and preventing water intrusion in between-slab construction.
A significant factor in preventing damage from moisture ingress is the use of high-quality weatherproofing materials like the PC2R Protection Course. These materials not only reduce maintenance costs but can also extend the life span of buildings and structures.
While these measures can significantly reduce moisture damage, they may not be enough on their own to completely protect concrete from the long-term effects of moisture exposure.
Role of Vapor Barriers and Moisture Mitigating Primers
Vapor barriers are another critical tool for achieving effective moisture control in concrete structures. These barriers, typically made of plastic sheeting, limit vapor transmission from below the ground up into slab-on-ground concrete floor systems. By reducing the amount of moisture migrating through the slab, vapor barriers delay the onset of concrete damage and prevent costly repairs down the road.
In addition to vapor barriers, moisture-mitigating primers can provide an added layer of protection against moisture intrusion. These epoxy-based primers are designed to be applied to damp concrete surfaces prior to installing flooring systems. Through chemical reactions with moisture in the concrete substrate, these primers work to form a barrier that helps reduce the migration of both moisture and alkaline salts into the flooring above.
Applying a primer to a damp concrete surface will simply trap moisture if the underlying issue isn’t addressed. However, allowing proper curing time for concrete is not always feasible when construction schedules are tight. This is where moisture-mitigating primers come into play, providing extra protection by reducing the chance of moisture wicking up through floors or walls.
Products like Dex-O-Tex’s VaporControl Primer 1P are effective as they can withstand internal vapor pressures up to 24 pounds per 1000 square feet per day while also promoting healthy indoor air quality, a critical factor for many commercial buildings that are occupied during construction.
While some may argue that products like vapor barriers and primers add additional costs to construction projects, neglecting these measures can lead to much higher costs associated with future repairs and replacements due to moisture damage.
With effective drainage, weatherproofing, protective coatings, vapor barriers, and primers all working together, builders can help ensure that their concrete structures stand up against even the most severe environmental factors for years to come.
Preventing Moisture Damage: Best Practices
Moisture is the primary cause of concrete damage, and that's why a proper prevention plan should be put in place. It’s crucial to take note of specific best practices to keep moisture at bay, ensuring optimal durability for your concrete structures.
One of the best ways to prevent moisture damage is to seal every possible exposure point. All entry points, like doors, windows, vents, and pipes, should be adequately sealed with the right sealant to make them watertight.
Using a waterproof coating on the concrete surface helps as well. Ensure that you opt for top-quality coatings that will guarantee long-lasting results. An effective coating not only protects against water vapor penetrating but also provides an additional layer of protection against chemicals and other debris.
Another approach is to grade all exterior surfaces surrounding your concrete structure away from it so that excess water drains away from the area. This action helps establish a natural drainage system, minimizing the potential for moisture accumulation around your structure.
Applying a regular maintenance schedule significantly reduces the risk of moisture damage to your concrete surface. Make sure that you regularly inspect your structure for any signs of wear or tear. Simple things like sealing cracks on time can go a long way in preventing more significant issues down the road, such as concrete erosion, which can lead to structural instability.
The placement of water-absorbent materials near your concrete establishment should be avoided altogether or kept far away from the building’s foundation. Materials such as mulch, dry leaves, and soil have a high moisture content and are capable of absorbing rainwater splashes, thus allowing water vapor to be released into the air towards the ground component.
Moisture in concrete can cause a lot of damage, but don't worry; Allsource Supply Inc. has the right answer. With our high-tech concrete moisture control goods, you can keep your concrete surfaces from splitting, coming apart, and growing mold because of water. Our moisture control systems make a shield that keeps water from getting into your concrete and makes sure that it will last for a long time.
Trust our knowledge to help you deal with moisture problems and protect your property. Whether it's for a home or a business, our innovative methods for controlling moisture will give you peace of mind and keep your concrete in great shape for years to come. Don't let water damage your concrete! Allsource Supply Inc. has the best tools and knowledge for controlling water. Contact us.